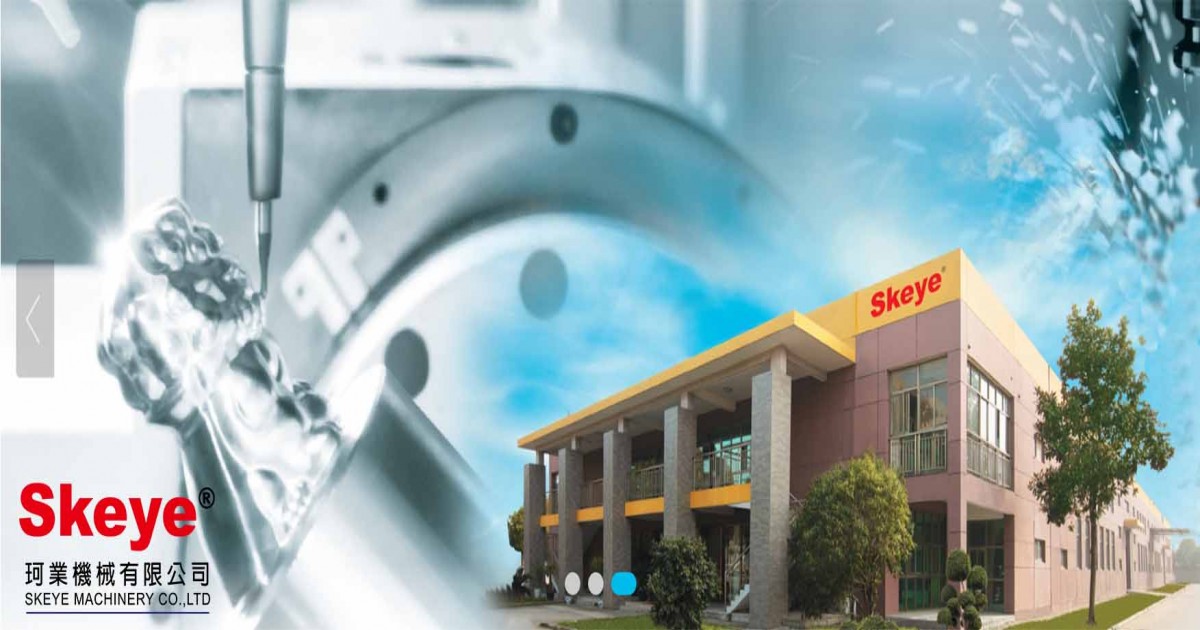
angle head holder
The angle milling head is abbreviated as the angle head, which is a commonly used accessory to expand the functions of the machine tool. Its accuracy is directly related to the machining accuracy of the machine tool. After the angle head is installed on the machine tool, the tool rotation center line can be angled with the spindle rotation center line to process the workpiece. The use of the angle head can increase the processing range and adaptability without changing the structure of the machine tool, achieving stability, low noise, large torque, and high temperature resistance. Long-life operation realizes vertical-horizontal conversion five-sided machining and specific angle bevel machining. When it is difficult to fix large workpieces, when used in simple machining, precision workpieces are fixed at one time, and when multiple faces need to be machined; relative to the reference plane, carry out any angle During processing; the processing is maintained at a special angle for profiling milling, such as ball end milling; the hole in the hole, the milling head or other tools cannot penetrate the hole to process the small hole; the oblique hole, which cannot be processed by the machining center, Chutes, etc., such as the internal holes of the engine and the case. For angle heads that are difficult to turn over for some large workpieces or require high-precision tool holder connection methods, you only need to install the positioning block required for angle head positioning on the end face of the machine spindle to realize the use of angle heads. The angle head greatly expands the machine tool. Performance.
The high-end and the forefront of technology in the field of angle heads; whether heavy cutting or high-speed precision machining, angle heads are mainly used in machining centers, and the installation is very simple and convenient. The machine does not need any changes to the gantry boring and milling machine and the vertical lathe, and can be installed on the tool In the library, the tool can be automatically changed between the tool magazine and the machine tool spindle; medium and heavy-duty have greater rigidity and torque, which can be suitable for heavy cutting processing needs. Technology can provide you with standard and tailor-made angle head processing solutions to solve your processing problems and improve production efficiency and processing accuracy.
In the vertical machining center, the processed products with very large workpieces are often encountered, and the shapes are relatively special, and it is difficult to fix them. For such processed parts, if they are not sufficiently fixed, the processing will not be carried out smoothly. . Moreover, when the Z axis of the machining center cannot reach the workpiece during operation, the power of the angle head must be used to complete the machining process. Because the use of the angle head can greatly increase the flexibility of the machining center and make up for its shortcomings.
Although the current machining tools have become very diversified, the shapes of the machined parts have become more and more weird, and there are still many machined parts that can not be processed with suitable tools. For example, hole-in-hole machining and groove-in-groove machining are too narrow in space and complicated in structure, so traditional machining methods cannot be used to process them at all. At this time, you can also use the angle head to complete the processing.
The use of stainless steel as the material of the angle device can effectively improve its performance and rust. At the same time, in order to facilitate the installation and debugging of the angle head, the gear replacement process is adopted. This small measure is greatly improved. This improves the accuracy of the angle head processing accessories, and at the same time extends its life.
Find out the machine parameters: brand, model, vertical/horizontal, spindle type, spindle tool connection method (HSK, BT, CAT, SK), presence or absence of coolant (whether it is supplied from the spindle center and its pressure), spindle power, spindle Torque Nm, maximum spindle speed, maximum tool carrying weight, tool magazine type, automatic tool change, maximum allowable tool length. Check the angle head parameters: tool clamping method (ER, MI quick change, high-precision hydraulic clamping, powerful jacket clamping, disc milling cutter, etc.), speed RPM, torque, cooling method (no cooling, internal cooling, external cooling, etc.) , The internal cooling water is discharged from the center of the tool) and so on.
*The precise positioning block of the angle head plays a role in positioning the angle head. The measurement method is very simple. Just place it on the marble platform and compare the positioning block with it to see if its parallelism is within the range required by the standard. .
Before each processing, the position of the angle head must be fixed at a position suitable for processing the workpiece. However, repeated processing can easily lead to inaccurate parallelism of the positioning block. At this time, it must be measured first. Then make corrections.
*The spindle on the precision angle head machine is connected with the machine through the flange. The accuracy of the flange surface is measured and calibrated. When measuring, you only need to place the micrometer on the worktable of the machine to measure the method. If the accuracy of the flange surface exceeds the standard range, a new flange needs to be replaced and reconnected. In the case of high-speed operation, the accuracy of the flange surface is prone to wear, which will cause problems with the rotation of the spindle.
*The accurate flange surface of the angle angle head is realized by screws when connecting with the machine. When checking the accuracy of the flange surface, also check the situation of the screws by the way. Sometimes the flange accuracy is not due to the flange itself. It is caused by the loosening of the screws. The screws are prone to wear during long-term vibration. The most common is the wear of the teeth. If the screws are worn out, the general maintenance is of little significance, and new screws must be replaced.
Precautions for using angle head
1. When the axis of the inclined hole is parallel to any one of the X, Y, and Z axes of the machine tool, the machine tool should have the linkage function of more than two axes before it can be used.
2. When the axis of the inclined hole is not parallel to the X, Y, and Z axes of the machine tool, the machine tool should have the linkage function of three or more axes before it can be used.
3. Before working, the angle head needs to run for 5-10 minutes at 500 rpm.
4. The working temperature of the angle head is 50 degrees.
There are many types of angle heads
The first type, single output angle head
This is the most frequently used type. It is easy to automatically change the tool during use, and it can have a relatively large cutting rigidity. It can perform deep hole processing on mechanical product workpieces. Its biggest feature is that it can be manufactured. The light-weight angle head side milling head is easy to program and process, which can reduce interference to the workpiece or the machine.
The second type, dual-output angle head, multi-output angle head
The dual output corresponding to the single output, that is, the dual output angle head or the multiple output angle head. This is a further improvement and improvement on the basis of single output. It can make up for the shortcomings of the former. It can output in the same direction or output in different directions. Its biggest advantage is that it eliminates the need for processing in the opposite direction during processing. Manual adjustment is troublesome, so it has a great effect on improving processing efficiency and production efficiency, but it will cause interference during processing, and the size will be larger than that of a single output angle head. Relative rigidity is not as good as a single output angle head.
The third type, offset angle head
Offset is mainly because the centerline of rotation of the tool and the centerline generated when the spindle on the machine tool rotates are on two different surfaces. This design is more suitable for special processing requirements. If a certain processing part needs to be adjusted within a certain range during processing, this type of angle head can be used, because it has a certain installation space and working space in a certain direction Is reserved for adapting to changes in the processing process. This kind of angle head is special and suitable for work pieces and machines with interference.
The fourth type, adjustable angle head
is an adjustable angle head that combines the functions and characteristics of the first four angle heads, or we can call it a universal angle head or a universal angle head. In other words, it can change the processing angle at will. This kind of angle head can process any angle, but every time you process, you still need to type a table to determine the angle. This kind of angle head can replace the fourth axis, and the price is more favorable than the fourth axis.
Angle head technology
*Geometric tolerance requirements for the accuracy of the angle head machining bearing seat
*High-precision head shaft degree requirements for the arc surface of the angle head bearing seat
*High-precision straightness requirements for angle head single or multiple bearing seats
Angle head installed on the machine
*The combination of angle head fixed seat frame and positioning bolt corresponds to all positioning blocks. Now you can use the original positioning block next to the spindle as usual. The installation types include straight round hole, straight groove, tapered groove, and tapered hole.
Angle head positioning bolt type
*Angle head straight shank bolt-mainly used for drilling and tap processing-can be supplied with coolant
*Angle head straight handle opening bolt-There is no gap with the positioning block, the combination is stronger-ATC tool change is not possible
*Angle head taper pin-the taper pin is pressed by elastic force, and the positioning is really firm.
https://www.skeye.com.tw/